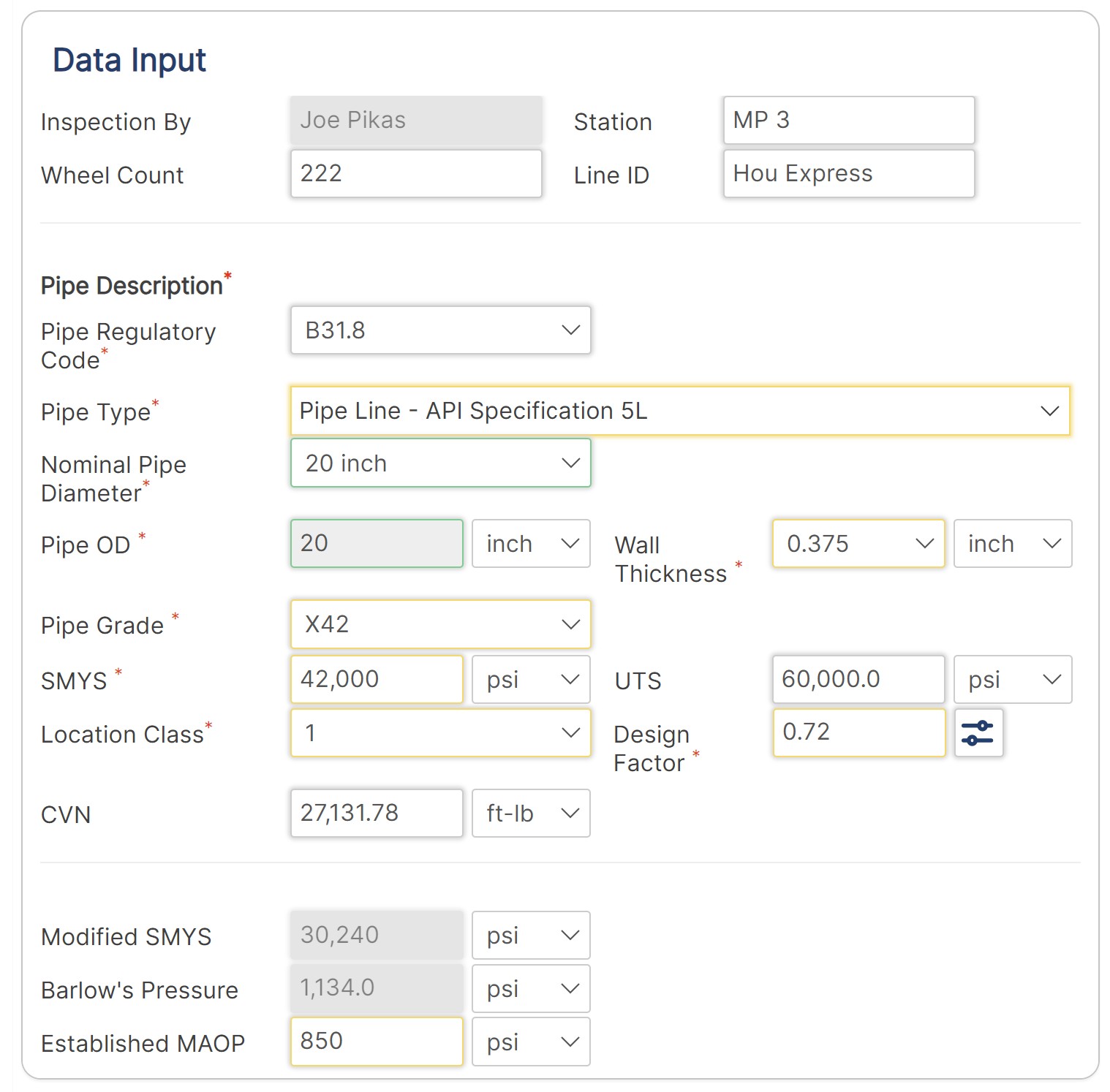
Definitions
- Barlow’s Pressure
- Relates the internal pressure that a pipe can withstand to its dimensions and the strength of its materials.
- CVN
- This is the full size specimen (10 mm x 10 mm) Charpy V-notch upper shelf energy of the pipe material. This is only used in the crack-like assessment algorithm and is not required for the corrosion assessment.
- Corrosion Depth
- User selects corrosion depth (pit depth) data from ILI (in-Line Inspection) as the basis of the calculation
- Corrosion Growth Rate
- User-defined parameter used for remaining life and re-assessment interval calculations
- Established MAOP
- User-defined Maximum Allowable Operating Pressure (MAOP)
- Factor – Design Factor
- User-specified design factor of the pipe to perform RSTRENG calculations
- Geographical Location
- This location (Latitude/Longitude) can either be of the pipe or the defect itself. The icon beside this input field is used to select a point on the Map
- In-Line-Inspection (ILI)
- Evaluation of pipes and pipelines that utilize non-destructive examination techniques to detect and size internal damage.
- Inspection By
- The name on the user account is displayed in this field which is a non-editable field
- Line ID
- User input data used for identification
- Location of Pitting
- Captures the location of pitting data as entered by the user
- Measurement Method
- The user specifies whether the data provided will be Corrosion depth or the remaining wall thickness which is supported by the RSTRENG application
- Modified SMYS
- A calculated value that is given by SMYS * F – Design Factor
- P Design (Barlow
- P – Design/Design Pressure/Barlow’s Pressure is calculated using (2*SMYS* thickness*F) / OD.
- Pipe OD
- User input data for the outside diameter of the pipe for RSTRENG assessment
- Pipe Regulatory Code
- Allows user to select the regulatory code for pipe operations. The selection from the regulatory code option is used to govern the Design Factor entry. Currently the dropdown selection for regulatory code includes ASME B31.8, ASME B31.4, CSA Z662 and User Defined. When User Defined is selected, the Design Factor can be a manual entry.
- Pipe Type
- Allows user to select the pipe catalog to be used in the model. If “Custom Pipe” is selected, user can manually enter Pipe OD, Wall Thickness and SMYS.
- SMYS
- User input data for Specified Minimum Yield Strength (SMYS) of the pipe used for RSTRENG calculations
- Station Number/Mile Post
- User input data used for identification
- UTS
- User-specified data for Ultimate Tensile Stress (UTS) used in additional Maximum safe pressure Calculations
- Ultrasonic Thickness Meter (UTM)
- Non-destructive testing method used to inspect the metal thickness of ship hulls, piping and structural steel.
- Wall Thickness
- User input data for wall thickness of the pipe used for assessment
FAQ
-
Technical Toolboxes receives many RSTRENG questions throughout the year; however, most of them are not related to operating the software. These questions are related to procedures, definitions, and field repairs.
When metal loss features in pipelines are detected by in-line inspection (ILI), a decision to replace, repair, and assess remaining features. This decision is based on the prediction of the failure pressure of the corroded pipeline and must adhere to the US Code of Federal Regulations (CFR) Title 49, Parts 192 and 195, that stipulates that ASME B31G or RSTRENG be used to assess the remaining strength of corroded pipelines. Check Out
-
What Actions must be Taken to Address Integrity Issues?
According to DOT 192.933 a calculation of the remaining strength of the pipe shows a predicted failure pressure less than or equal to 1.1 times the maximum allowable operating pressure at the location of the anomaly. Suitable remaining strength calculation methods include, ASME/ANSI B31G; RSTRENG; or an alternative equivalent method of remaining strength calculation. Check Out
-
A corrosion rate needed to set the re-inspection interval, reassess the performance metrics and their current applicability, plus to ensure the assumptions made are correct. At each direct examination where corrosion pitting is found, the operator should measure and record each pitting cluster. The aforementioned data are then used to estimate corrosion rates. Average corrosion rates are related to the environment, depth of pitting and years of in-service. Check Out
-
Internal corrosion is most likely to occur where water first accumulates. Predicting these locations of water accumulation serve as a method for prioritizing local examinations. Predicting where water first accumulates requires knowledge about the multiphase flow behavior in the pipe requiring certain data. The following are some general calculations based on flow conditions. Keep in mind that these are strictly estimates and do not consider the effects of temperature, wettability, MIC, pressure, hydrocarbon characterization, gas composition, etc. Check Out
-
All corrosion defects found during each direct examination should be measured, documented, and remediated as needed. At each excavation, the pipeline operator should measure and record generic environmental characteristics (such as soil resistivity, hydrology, drainage etc.). These data have been used to estimate corrosion rates. Average corrosion rates related to soil resistivity are below in the following table with no CP. Check Out
-
ASME B31.G Original and Modified (0.85) are Level 1 assessment along with most other metal loss calculations that are limited to pits and short lengths of pitting clusters. Check Out