Orifice Flow Equation
The accepted one-dimensional equation for mass flow through a concentric, square edged orifice meter is stated in the Equations below. The derivation is based on conservation of mass and energy, one-dimensional fluid dynamics, and empirical functions such as equations of state and thermodynamic process statements. Any derivation is accurate when all the assumptions used to develop it are valid. As a result, an empirical orifice plate coefficient of discharge is applied to the theoretical equation to adjust for multidimensional viscous fluid dynamic effects. In addition, an empirical expansion factor is applied to the theoretical equation to adjust for the reduction in fluid density that a compressible fluid experiences when it passes through an orifice plate.
The fundamental orifice meter mass flow equation is as follows:
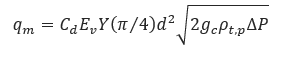
Where:
ππ β Mass Flow Rate
πΆπ β Orifice Plate Coefficient of Discharge
π β Orifice Plate Bore Diameter [in]
πΈπ£ β Velocity Approach Factor
βπ β Orifice Differential Pressure ,in ,π»-2.0.at 60β
π β Universal Constant=3.14159
π β Expansion Factor
ππ β Dimensional Conversion Factor
π
π‘,
πΒ β Density of the Fluid at Flowing Conditions (π
π,π
π)
The orifice meter is a mass meter from which a differential pressure signal is developed as a function of the velocity of the fluid as it passes through the orifice plate bore. Manipulation of the density variable in the equation permits calculation of flow rate in either mass or volume units. The volumetric flow rate at flowing (actual) conditions can be calculated using the following equation:
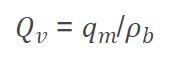
The volumetric flow rate at base (standard) conditions can be calculated using the following equation:
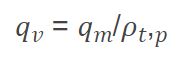
The mass flow rate (π
π) can be converted to a volumetric flow rate at base (standard) conditions (π
π£) if the fluid density at the base conditions (π
π) can be determined or is specified.
Orifice Plate Bore Diameter
The orifice plate bore diameter, d. is defined as the diameter at flowing conditions and can be calculated using the following equation:

π β Orifice Plate Bore Diameter [in]
ππ β Mean Orifice Bore Diameter [in]
πΌ
1Β β Linear Coefficient of Thermal Expansion of Orifice Plate Material [in/inββ]
π‘
πΒ β Flowing Gas Temperature [β]
π
πΒ β Reference Temperature Prifice Plates/Tubes [β]
The meter tube internal diameter, D, is defined as the diameter at flowing conditions and can be calculated using the following equation:
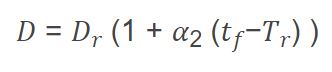
π· β Meter Tube Internal Diameter [in]
π·
πΒ β Mean Meter Tube Diameter [in]
πΌ
2Β β Linear Coefficient of Thermal Expansion of Meter Tube [in/inββ]
π‘
πΒ β Flowing Gas Temperature [β]
π
πΒ β Reference Temperature Prifice Plates/Tubes [β]
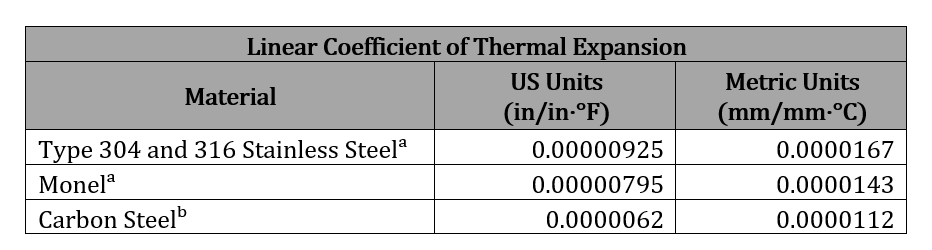
Note: For flowing temperature conditions outside those stated above and for
other materials, refer to the American Society for Metals Handbook.
α΅For flowing conditions between -100Β°F and +300Β°F, refer to ASME PTC 19.5.
α΅For flowing conditions between -7Β°F and + 154Β°F, refer to API Manual of
Petroleum Measurement Standards, Chapter 12, Section 2.
Empirical Coefficient of Discharge Equation for Flange-Tapped Orifice Meters
The concentric, square-edged, flange-tapped orifice meter coefficient of discharge, ,πΆ-π.(FT), equation, developed by Reader-Harris/Gallagher (RG), is structured into distinct linkage terms and is considered to best represent the current regression data base. The equation is applicable to nominal pipe sizes of 2 inches (50 millimeters) and larger; diameter ratios (π½) of 0.1-0.75, provided the orifice plate bore diameter, d” is greater than 0045 inch (11.4 millimeters); and pipe Reynolds numbers (,π
π-π·.) greater than or equal to 4000.
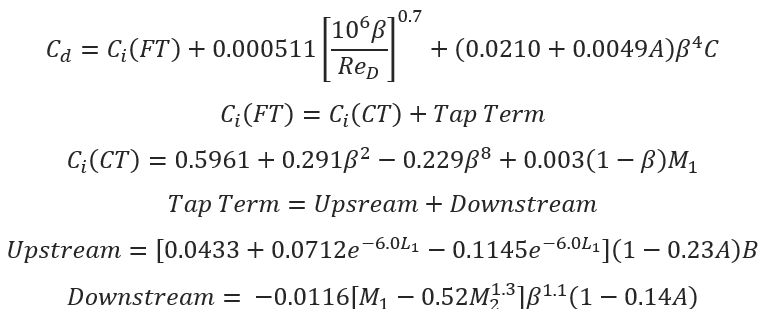
Where:
π½ β Diameter Ratio= ,π-π·.
πΆ
π(πΉπ) β Coefficientof Discharge at a Specific Reynolds number for FlangeβTapped Orifice Meter
πΆ
π(πΉπ) β Coefficientof Discharge at infinite Reynolds number for FlangeβTapped Orifice Meter
πΆ
π(πΆπ) β Coefficientof Discharge infinite Reynolds number for CornerβTapped Orifice Meter
πΏ
1Β β dimentionless correction for the tap location
π β Napoerian Constant=2.71828
π
4Β = 1.0 when D is in Inches=25.4 when D is in millimeters
π
π
π·Β β pipe Reynolds number
Reynoldβs Number
The RG equation uses pipe Reynolds number as the correlating parameter to represent the change in the orifice plate coefficient of discharge, Cd, with reference to the fluid’s mass flow rate (its velocity through the orifice), the fluid density, and the fluid viscosity. The pipe Reynolds number can be calculated using the following equation:
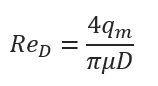
π· β Meter Tube Internal Diameter [in]
π β Universal Constant=3.14159
π
πΒ β Mass Flow Rate
π
π
π·Β β pipe Reynolds number
π β Absolute Viscosity of Fluid
Velocity of Approach Factor
The velocity of approach factor,Β πΈ
π£, is calculated as follows:
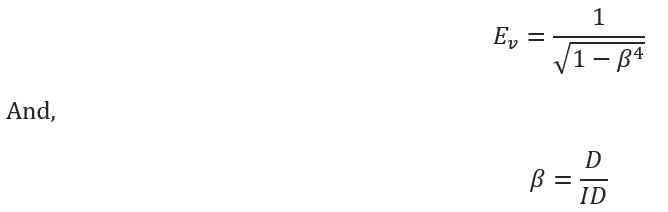
Where:
π½ β Diameter Ratio
πΈ
π£Β β Velocity Approach Factor
π β Orifice Plate Bore Diameter ,in.
π· β Meter Tube Internal Diameter [in]
This assumption defines the expansion as reversible and adiabatic (no heat gain or loss). Within practical operating ranges of differential pressure, flowing pressure, and temperature, the expansion factor equation is insensitive to the value of the isentropic exponent. As a result, the assumption of a perfect or ideal isentropic exponent is reasonable for field applications.
The application of the expansion factor is valid if the following dimensionless pressure ratio criteria are followed:
Where:
π
3Β β Unit Conversion Factor
π
π1Β β Absolute Static Pressure at Upstream Tap [psi]
π
π2Β β Absolute Static Pressure at Downstream Tap [psi]
βπ β Orifice Differential Pressure [in π»
20] at 60β
Upstream/Downstream Expansion Factor
The upstream expansion factor requires determination of the upstream static pressure, the diameter ratio, and the isentropic exponent. If the absolute static pressure is taken at the upstream differential pressure tap, then the value of the expansion factor, π
1Β , shall be calculated as follows:

When the upstream static pressure is measured,
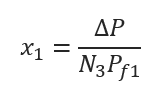
When the downstream static pressure is measured,
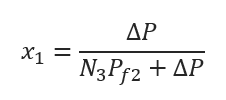
π
1Β β Upstream Expansion Factor
π
3Β β Unit Conversion Factor
π₯
1Β β Ratio of Differential Pressure to Asolute Static Pressure
π
π1Β β Absolute Static Pressure at Upstream Tap [psi]
π
π2Β β Absolute Static Pressure at Downstream Tap [psi]
βπ β Orifice Differential Pressure ,in ,π»-2.0.at 60β
π β Isentropic Exponent
π½ β Diameter Ratio
The downstream expansion factor requires determination of the downstream static pressure, the upstream static pressure, the downstream compressibility factor, the upstream compressibility factor, the diameter ratio, and the isentropic exponent. The value of the downstream expansion factor, π2, shall be calculated using the following equation:
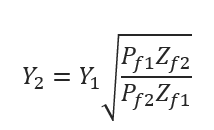
When the upstream static pressure is measured,
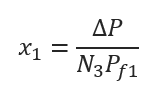
When the downstream static pressure is measured,
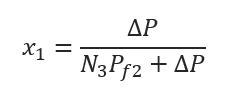
π
1Β β Upstream Expansion Factor
π
2Β β Downstream Expansion Factor
π
3Β β Unit Conversion Factor
π₯
1Β β Ratio of Differential Pressure to Asolute Static Pressure
π₯
1/π β Upstream Acoustic Ratio
π
π1Β β Absolute Static Pressure at Upstream Tap [psi]
π
π2Β β Absolute Static Pressure at Downstream Tap [psi]
π
π1Β β Fluid Compressibility at Upstream Tap [psi]
π
π2Β β Fluid Compressibility at Downstream Tap [psi]
βπ β Orifice Differential Pressure ,in ,π»-2.0.at 60β
π β Isentropic Exponent
Input Parameters
- To create a new case, click the βAdd Caseβ button
- Select the AGA 3 β Volume Flow Rate Calculation β Method I application from the Regulators & Meters module list.
- Enter Case Name, Location, Date and any necessary notes.
- Fill out all required fields.
- Make sure the values you are inputting are in the correct units.
- Click the CALCULATE button.
- Molecular Weight
- Static Pressure Measurements are Taken from the
- Linear Coefficient of Thermal Expansion
- Reference Temperature Orifice Plates/Tube
- Compressibility Factor at Flowing Conditions
- Compressibility Factor at Base Conditions
- Compressibility Factor at Standard Conditions
- Mean Orifice Bore Diameter
- Mean Meter Tube Internal Diameter
- Real Gas Relative Density
- Differential Pressure [in.H2O] at 60 deg F
- Base Pressure
- Static Pressure
- Contract Base Temperature
- Flowing Gas Temperature
- Carbon Dioxide
- Nitrogen
- Gas Dynamic Viscosity
- Isentropic Exponent
Outputs/Reports
- View the results.
- If an input parameter needs to be edited be sure to hit the CALCULATE button after the change.
- To SAVE, fill out all required case details then click the SAVE button.
- To rename an existing file, click the SAVE As button. Provide all case info then click SAVE.
- To generate a REPORT, click the REPORT button.
- The user may export the Case/Report by clicking the Export to Excel/PowerPoint icon.
- To delete a case, click the DELETE icon near the top of the widget.
- Orifice Diameter
- Tube Diameter
- Diameter Ratio
- Velocity Approach Factor
- Expansion Factor
- Reynolds Number
- Coefficient of Discharge
- Flow Rate at Standard Conditions
- Flow Rate at Base Conditions
Related Links