Introduction
The Colebrook-White equation is recommended for use by those unfamiliar with pipeline flow equations. It will produce the greatest consistency of accuracy over the widest possible range of variables. The Colebrook Equation has good accurate results for lower flow rates (150-250 MMSCFD); However, larger errors exist above a 250 MMSCFD flow rate.
The friction factor is solved using the Newton-Raphson method.
f=\frac{64}{Re};\,Laminar\,Flow: Re < 2000 \~\ \frac{1}{\sqrt{f}}=2\log_{10}(Re\sqrt{f})-0.8;\,Smooth\,Pipe:Re >4000\,and\,\frac{\varepsilon}{D}\rightarrow0\~\ \frac{1}{\sqrt{f}}=-2\log_{10}\biggr(\frac{\varepsilon}{3.7D}+\frac{2.51}{Re\sqrt{f}}\biggr);\,Transitional,\,Colebrook-White\,Eq,Re>4000\~\ \frac{1}{\sqrt{f}}=1.14-2\log_{10}\biggr(\frac{\varepsilon}{D}\biggr);\,Wholly \,Rough
f=\frac{64}{Re};\,Laminar\,Flow: Re < 2000 \\~\\ \frac{1}{\sqrt{f}}=2\log_{10}(Re\sqrt{f})-0.8;\,Smooth\,Pipe:Re >4000\,and\,\frac{\varepsilon}{D}\rightarrow0\\~\\ \frac{1}{\sqrt{f}}=-2\log_{10}\biggr(\frac{\varepsilon}{3.7D}+\frac{2.51}{Re\sqrt{f}}\biggr);\,Transitional,\,Colebrook-White\,Eq,Re>4000\\~\\ \frac{1}{\sqrt{f}}=1.14-2\log_{10}\biggr(\frac{\varepsilon}{D}\biggr);\,Wholly \,Rough
π β Friction Factor
D β Inside Pipe Diameter[in]
π β Pipe Roughness[in]
F=\sqrt{\frac{1}{f}}
F=\sqrt{\frac{1}{f}}
πΉ β Transmission Factor
Q=C_Q(\frac{T_b}{P_b})D^{2.5}F\biggr[ \frac{P_1^2-e^sP_2^2}{GT_fL_eZ} \biggr]^{0.5}
Q=C_Q(\frac{T_b}{P_b})D^{2.5}F\biggr[ \frac{P_1^2-e^sP_2^2}{GT_fL_eZ} \biggr]^{0.5}
π β Flow Rate (FT3/day)
πΆπ β 38.774
ππ βTemperature Base (Β°R)
ππ β Pressure Base (psia)
ππ β Gas Flowing Temperature (Β°R)
π· β Internal Diameter (in)
πΉ β Transmission Factor
π β Pipe Roughness
π1 β Upstream Pressure (psig)
π2 β Downstream Pressure (psig)
πΊ β Gas Specific Gravity
π β Compressibility Factor
Le β Pipe Segment Length including Expansion (mi)
s=\frac{C_S\triangle HG}{T_fZ}
s=\frac{C_S\triangle HG}{T_fZ}
π β Elevation adjustment parameter
πΆπ β 0.0375
π β Compressibility Factor
ππ β Gas Flowing Temperature (Β°R)
βπ»πΊ β Change in Elevation (ft)
L_e=\frac{(e^s-1)}{s}
L_e=\frac{(e^s-1)}{s}
πΏπ β Pipe Segment Length including Expansion (mi)
π β Elevation adjustment parameter
V=0.75\frac{Q_h}{D^2P_{avg}}
V=0.75\frac{Q_h}{D^2P_{avg}}
π β Velocity (ft/sec)
πβ β Volumetric flow rate (scf/hr)
π· β Internal Diameter (in)
πππ£π β Average Pipeline Pressure (psia)
For Small Pressure Drop P2 > 0.8 P1:
P_{avg}=\frac{(P_1-P_2)}{2}
P_{avg}=\frac{(P_1-P_2)}{2}
For Large Pressure Drop:
P_{avg}=\frac{2}{3}\biggr[ P_1+P_2-\frac{P_1P_1}{P_1+P_2} \biggr]
P_{avg}=\frac{2}{3}\biggr[ P_1+P_2-\frac{P_1P_1}{P_1+P_2} \biggr]
Case Guide
Part 1: Create Case
- Select the Colebrook-White application in the Hydraulics module.
- To create a new case, click the βAdd Caseβ button.
- Enter Case Name, Location, Date and any necessary notes.
- Fill out all required parameters.
- Make sure the values you are inputting are in the correct units.
- Click the CALCULATE button to overview results
Input Parameters
- Temperature base(Β°F)
- Pressure base(psia)
- Gas Flowing Temperature(Β°F)
- Gas Specific Gravity
- Compressibility Factor
- Pipeline Efficiency Factor
- Upstream Pressure(psig)
- Downstream Pressure(psig)
- Flow Rate(Barrels per Day)
- Internal Pipe Diameter(in)
- Length of Pipeline(mi)
- Upstream Elevation(ft)
- Downstream Elevation(ft)
Downstream Pressure
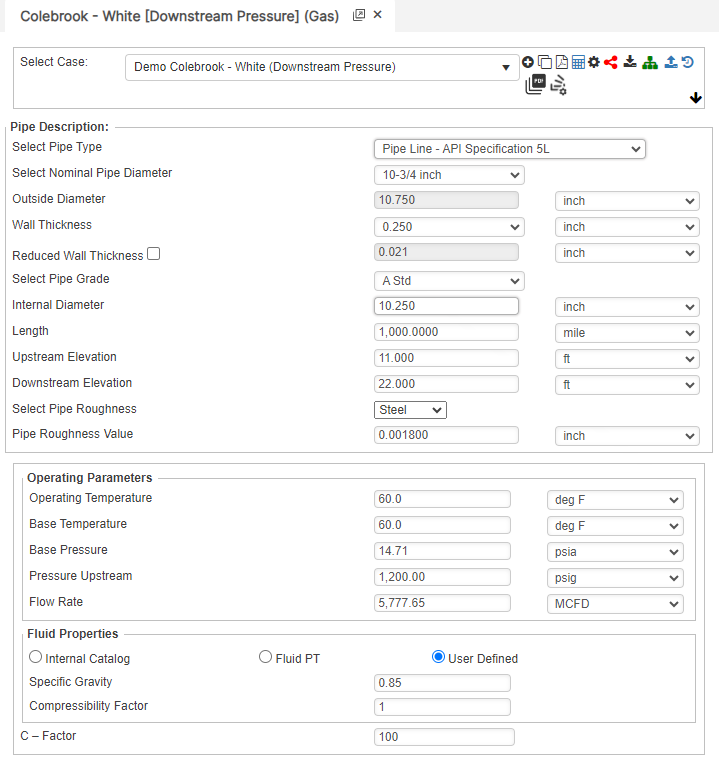
Flow Rate
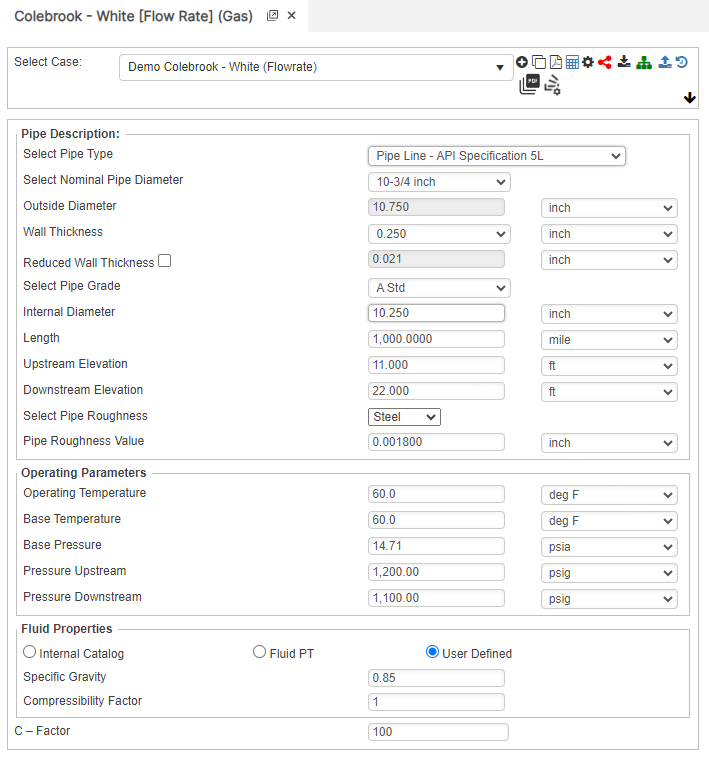
Internal Pipe Diameter
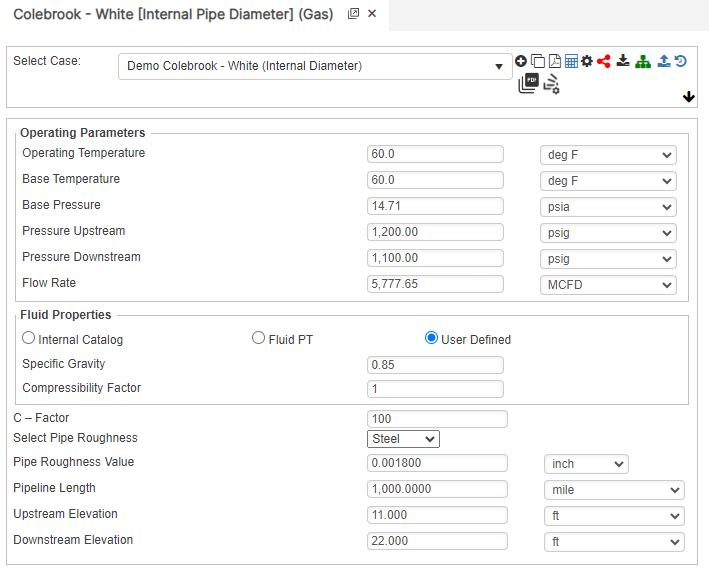
Upstream Pressure
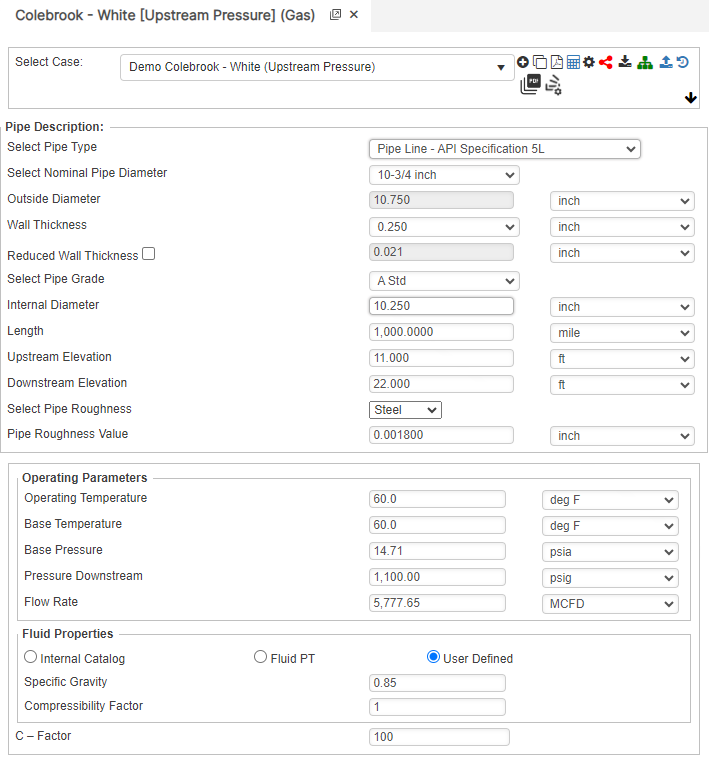
Part 2: Outputs/Reports
- If you need to modify an input parameter, click the CALCULATE button after the change.
- To SAVE, fill out all required case details then click the SAVE button.
- To rename an existing file, click the SAVE As button. Provide all case info then click SAVE.
- To generate a REPORT, click the REPORT button.
- The user may export the Case/Report by clicking the Export to Excel icon.
- To delete a case, click the DELETE icon near the top of the widget.
Results
- Downstream Pressure(psig)
- Flow Rate(ft/sec.)
- Internal Pipe Diameter(in)
- Upstream Pressure(psig)
- Transmission Factor
- Velocity(ft/sec.)
- Erosional Velocity
- Sonic Velocity
Downstream Pressure

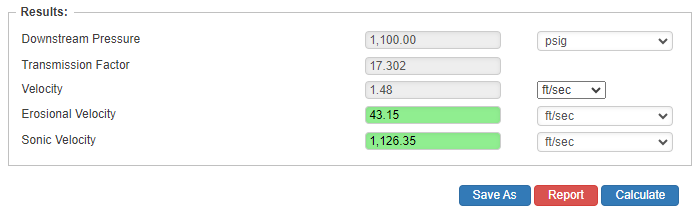
Flow Rate

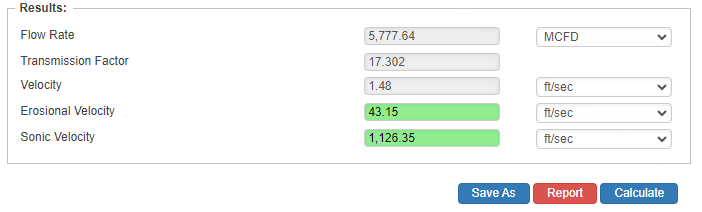
Internal Pipe Diameter

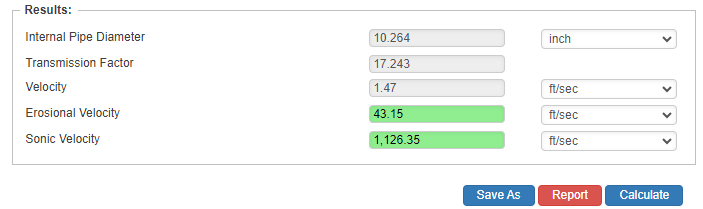
Upstream Pressure

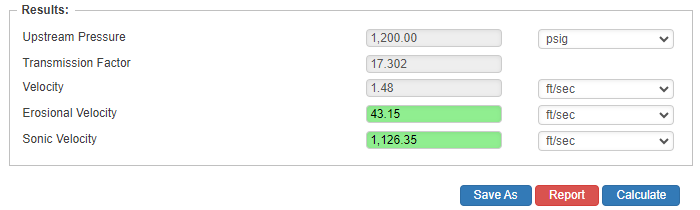
References
- βPipeline Rules of Thumbβ Gulf Professional Publishing, Seventh Edition, McAllister, E. W.
- βGas Pipeline Hydraulicsβ, Systek Technologies, Inc., Menon, Shahi E.
- βAdvanced Pipeline Designβ, Carroll, Landon and Hudkins, Weston R.
- American Gas Association (AGA), βReference: Eq-17-18, Section 17, GPSAβ, Engineering Data Book, Eleventh Edition
- Hydraulic Transients, McGraw-Hill, New York., Streeter, V.L. and Wylie, E.B. (1967)
- Water Hammer Analysis. Jour. Hyd. Div., ASCE., Vol. 88, HY3, pp79-113 May, Streeter, V.L. (1969)
- Unsteady flow calculations by numerical methodsβ, Jour. Basic Eng., ASME., 94, pp457-466, June. Streeter, V.L. (1972),
- Hydraulic Pipelines, John Wiley & Sons, J. P Tullis (1989)
FAQ
-
Purging is a process of removing gas from the pipeline. Controlled purging of gases from pipelines by direct displacement with other gases that have been safely practiced for many years with the recognition that some flammable mixture is present. Purging of gases from pipelines by direct displacement with another gas also has been similarly practiced. It works both ways; however, there will always be an atmosphere of type of a mixture. This is due to the densities of the gases. Check Out
-
Pipe erosion begins when velocity exceeds the value of C/SQRT(Ο) in ft/s, where Ο = gas density (in lb./ft3) and C = empirical constant (in lb./s/ft2) (starting erosional velocity). We used C=100 as API RP 14E (1984). However, this value can be changed based on the internal conditions of the pipeline. Check Out
-
The maximum possible velocity of a compressible fluid in a pipe is called sonic velocity. Oilfield liquids are semi-compressible, due to dissolved gases. Check Out