Introduction
The Level 1 analysis tool is intended for simple pipeline stability analyses. It calculates the static stability of an un-trenched pipeline against lateral and vertical displacement under wave and current loading. Drag, lift and inertia forces are considered along with the restraining effect of either cohesive or non-cohesive soils. This restraining effect is dependent on the soil friction factor and pipe submerged weight for non-cohesive soils, and on the cohesive shear strength and pipe embedment depth for cohesive soils. Any assumed embedment will also reduce the exposed drag area.
The Level 1 analysis is based on static conditions and a single frequency regular wave. Linear wave theory is used to transform wave parameters to near seabed water particle velocities. Wave induced water particle velocities are added to the bottom current, and forces on the pipe are calculated using Morison’s equation along with input force coefficients.
Assumptions associated with the Level 1 analysis include the following:
- Waves are assumed to be regular and unidirectional.
- Airy linear wave theory is used to describe wave kinematics.
- Hydrodynamic drag, lift, and inertial forces are calculated assuming a stationary pipe and a Morison type force formulation.
- The restraining force from a cohesive soil is independent from the pipe-seabed contact force
Level 1 analysis may typically be performed under the following circumstances:
- To obtain a simple, quick, reasonable estimate of historical concrete coating requirements.
- To check Level 2 or Level 3 analysis against a more conservative baseline, used in earlier designs.
Level 1 Input Data Tab
The Input Data tab allows the user to enter all the required parameter values for calculation, as presented in Figure 3-1.
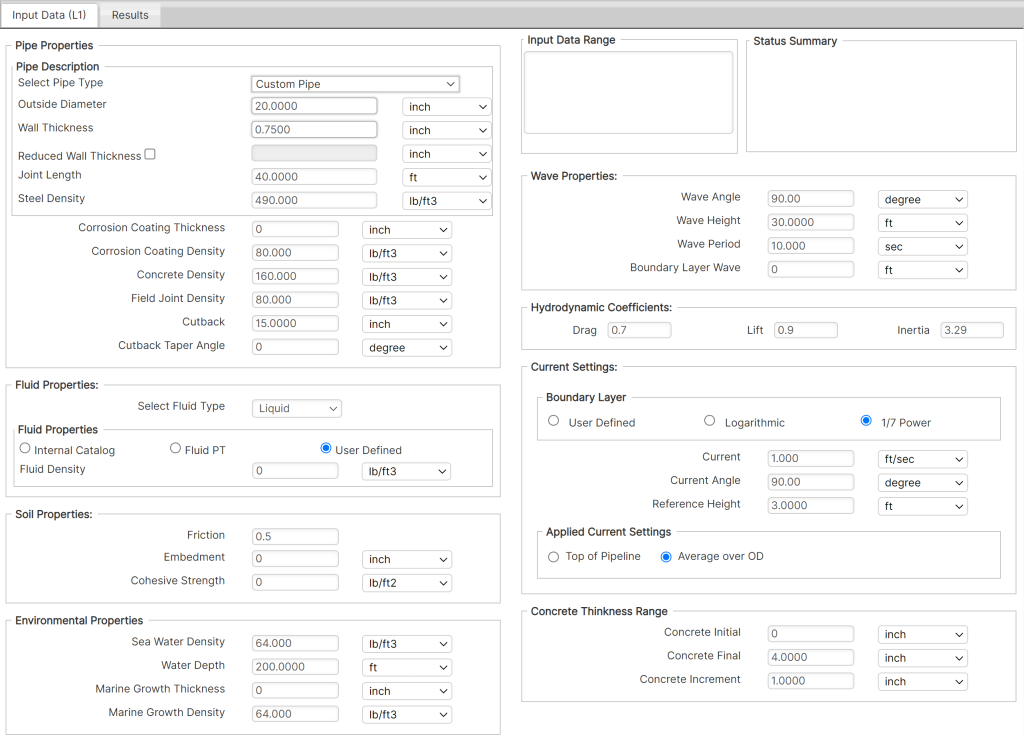
Pipe Properties
Outer Diameter -The outer diameter of the steel pipe.
Wall Thickness – The wall thickness of the steel pipe.
Corrosion Coating Thickness – Thickness of the external corrosion (or insulation) coating.
Corrosion Coating Density – Density of the external corrosion (or insulation) coating.
Concrete Density – Density of the external concrete weight coating.
Field Joint Density – Density of the field joint coating and infill.
Cutback – Cutback in the concrete coating at each end of the pipe joint, as presented in Figure 3-2.
Cutback Taper Angle – Taper angle of concrete coating, referenced from the radial direction, as presented in Figure 3-2.
Product Density – Density of the product/contents inside the pipeline.
Joint Length – The nominal length of one pipe joint.
Steel Density – Density of the steel pipe.
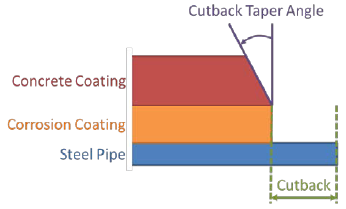
Wave Properties
Various parameters defining the wave are inputted in this area, with the basic definitions connected to a single regular wave presented in Figure 3-3.
It should be noted that for situations where the wave induced velocity becomes very small, results are not outputted. The user can overcome this issue by setting a combination of small wave height and large water depth to create a negligible but non-zero wave induced velocity. The use of unrealistically small peak period with this intent is not recommended.
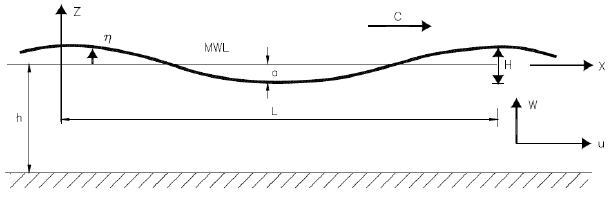
Where:
a – The wave amplitude, the difference in surface elevation between crest/trough and mean water level (MWL)
H – The wave height, the difference in surface elevation between the wave crest and trough (H = 2a in the case of a sinusoidal wave)
η – The surface elevation from MWL
L – The wave length, the horizontal distance between two successive crests
T – The period, the time interval between passage of two successive crests at a fixed point
h – The water depth
k – The wave number (k = 2π/L)
ω – The angular frequency (ω = 2π/T)
f – The wave frequency (f = 1/T = ω/2π)
s – The steepness, the ratio between wave height and length (s = H/L)
c – The wave propagation speed
Wave Angle – The angle of wave propagation relative to the pipeline (perpendicular to the pipe is 90°).
Wave Height – The vertical distance from wave trough to crest, as presented in Figure 3-3.
Wave Period – The time interval between successive wave crests passing a particular point.
Boundary Wave – The height of the boundary layer for waves, measured upwards from seabed. A diameter-averaged seventh power law formulation, the base formula of which is described in Boundary Layer, is used to calculate the wave velocity at the pipe.
Current Settings
Boundary Layer – Figure 3-4 presents a typical scenario where a pipeline diameter lies within the steady current boundary layer. Inclusion of current reduction due to its boundary layer can reduce the conservativeness in using free-stream current value.
The following options are provided in the software for the steady current boundary layer calculation (with the formulations below presented for a perpendicular current, for simplicity):
- User Defined: Uses the user defined current velocity as a constant value at the current angle for calculating current load.
U(z)=U_{UD}
U(z)=U_{UD}
- Logarithmic: Calculates the current load using a logarithmic relationship, given the current velocity, current angle, current reference height and seabed roughness.
\frac{U(z)}{U(z_r)} = \frac{\ln(z + z_0) – \ln(z_0)}{\ln(z_r + z_0) – \ln(z_0)}
\frac{U(z)}{U(z_r)} = \frac{\ln(z + z_0) - \ln(z_0)}{\ln(z_r + z_0) - \ln(z_0)}
- 1/7th Power: Calculates the current load using the 1/7th power law, given the current velocity, current angle and current reference height.
\frac{U(z)}{U(z_r)}=\left(\frac{z}{z_r}\right)^{\frac{1}{7}}
\frac{U(z)}{U(z_r)}=\left(\frac{z}{z_r}\right)^{\frac{1}{7}}
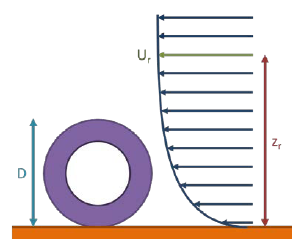
Current – The speed of the current, which acts at the reference height in the direction specified by the current angle.
Current Angle – The angle of attack at which the current acts on pipeline (perpendicular to the pipe is 90°).
Reference Height – The height above the seabed at which the current value is known (taken as the top of the boundary layer).
Seabed Roughness – Based on the seabed type Seabed roughness value can be input in this field. Reference can made from Table 3-1, as given in DNV-RP-F109 [2].
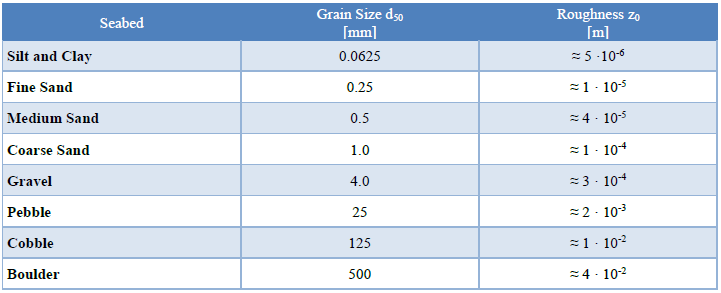
Applied Current Settings –
Selectable from the following options:
- Top of Pipeline: The applied current velocity is taken as the value calculated at the top of the pipe total diameter (being the pipe OD including all coatings and marine growth).
- Average over OD: The applied current velocity is taken as the average value experienced across the total OD.
Hydrodynamic Settings
Drag – Coefficient of drag force for the pipe.
Lift – Coefficient of lift force for the pipe.
Inertia – Coefficient of inertia force for the pipe.
Soil Properties
Friction – The lateral friction factor between the soil and the external surface of the pipe.
Pipe Embedment (Level 1) – Value of vertical embedment of the pipe into the soil.
Cohesive Strength (Level 1) – This shear strength value may be used in conjunction with friction for a cohesive soil, or simply specified as zero to represent a cohesion-less soil.
Environmental Properties
Seawater Density – Density of the seawater at the pipe location.
Water Depth – Depth of the sea from free surface to the seabed at the pipe location.
Marine Growth Density – Density of the marine growth on the external surface of the pipe.
Marine Growth Thickness (Level 1) – Thickness of the marine growth on the outermost surface of the pipe. This parameter is denoted here as tMG and illustrated in Figure 3-5 without embedment. Due to the various considerations of this parameter in the calculations, this value is treated slightly differently.
- Drag and Lift forces: these calculations include consideration of 1·tMG at the top of the pipe, as the dimensional consideration for these parameters is relevant to the exposed vertical pipe profile, with marine growth not being present on the underside of the pipe.
- Inertia force and submerged weight: these calculations consider a volume that includes 1·tMG circumferentially around the pipe, as the dimensional consideration for this parameter is relevant to the total volume, with the marine growth providing a volume almost equal to a full circumferential layer.
- KC Number: Level 1 calculates this value without the presence of marine growth or concrete coating.
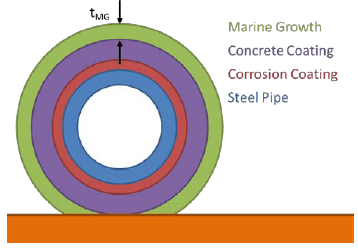
Concrete Thickness Range
Concrete Initial – The starting value of concrete thickness for the parameter incrementing, which represents its minimum value.
Concrete Final – The final value of concrete thickness for the parameter incrementing, which represents its maximum value.
Concrete Increment – The value at which the concrete thickness is incremented, from Initial value to Final value. The incremented values appear as separate entries in the outputs.
Level 1 Output Data Tab
The output can be viewed by clicking the Output Data (L1) tab, which displays the results outlined in this section in the chosen unit system, as presented in Figure 3-6. The outputs are also exported in PDF format. The PDF file can be opened by clicking on the Report button option in the ribbon menu.
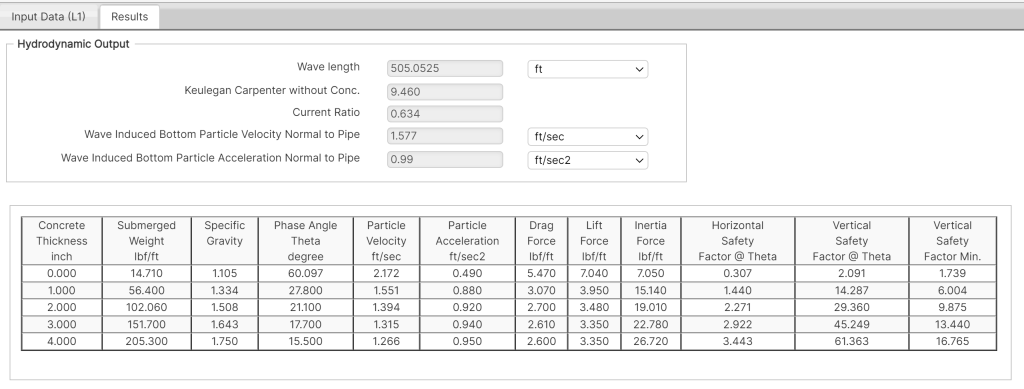
Hydrodynamic Outputs
Wave Length – The wave length is calculated based on the input wave properties, and describes the distance between successive wave crests.
Keulegan-Carpenter (without Concrete) – The Keulegan-Carpenter (KC) number calculated without considering a concrete coating on the pipe, which describes the relative importance in oscillatory flow of the drag forces over the inertia forces. The general form for the KC number is given by:
KC = \frac{U_{oscillatory} \cdot T}{D}
KC = \frac{U_{oscillatory} \cdot T}{D}
Where:
- Uoscillatory – The oscillatory velocity
- T – The period
- D – The outermost diameter under consideration (which excludes the concrete coating in this output column)
Current Ratio – The ratio of steady current to oscillatory current, considering the mean current over one pipe diameter:
\alpha = \frac{U_{steady}}{U_{oscillatory}}
\alpha = \frac{U_{steady}}{U_{oscillatory}}
Wave Induced Bottom Particle Velocity Normal to the Pipe – This field displays the wave bottom velocity perpendicular to the pipe; calculated using Airy wave theory.
Wave Induced Bottom Particle Acceleration Normal to the Pipe – This field displays the wave induced bottom acceleration perpendicular to the pipe; calculated using Airy wave theory.
Stability Results
Concrete Thickness – Displays the range of concrete thickness in the increments defined in the Input Data tab, with the first and last values in this column being the initial (minimum) and final (maximum) concrete thicknesses.
Submerged Weight – This column displays the submerged weight of the pipe, calculated for the respective concrete coating thickness in the leftmost column.
Specific Gravity – The ratio of the coated pipe density for the respective concrete coating thickness to the density of seawater.
Phase Angle Theta – The wave phase angle at which the minimum horizontal stability occurs.
Particle Velocity – The summation of the wave and current velocities acting at the pipe depth, for the phase angle.
Particle Acceleration – The normal particle acceleration acting at the pipe depth, for the phase angle.
Drag Force – The drag force corresponding to the particle velocity presented.
Lift Force – The lift force corresponding to the particle velocity presented.
Inertia Force The inertia force corresponding to the particle acceleration presented.
Horizontal Safety Factor at Theta – The minimum horizontal safety factor encountered across the full sweep of wave phase angle (which corresponds to the phase angle presented). It is the quotient of the available soil resistance divided by the sum of the horizontal forces.
Vertical Safety Factor at Theta – The vertical safety factor corresponding to the phase angle presented. It is the quotient of the pipe weight divided by the lift force.
Vertical Safety Factor – The minimum vertical safety factor encountered across the full sweep of wave phase angle, often not at the phase angle presented previously for the minimum horizontal safety factor.
Level 1 Reports
A PDF file is generated once an analysis is completed which can be accessed through the Report toolbar button. An instance of Level 1 report is shown in Figure 3-7.
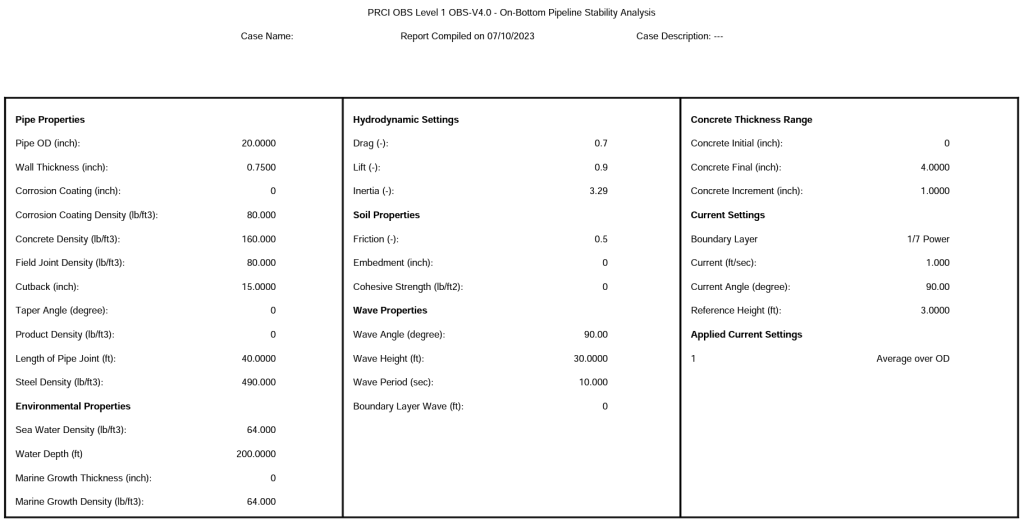

References
- Verley, R. L. P. and Lund, K. M. A Soil Resistance Model for Pipelines Placed on Clay Soils, OMAE – Volume 5, 1995
- DNV-RP-F109, On-Bottom Stability Design of Submarine Pipelines, Det Norske Veritas, Nov-2011
- Ochi, M. K. Hubble, E.N. Six-parameter wave spectra, Proceedings 15th International Conference on Coastal Engineering, Honolulu, 1976
- DNV-OS-F101, Submarine Pipeline Systems, Det Norske Veritas, Oct-2013
- On-Bottom Stability in Deep Waters Note, Det Norske Veritas
- Catalog No. L51522e, PR-170-185, Hydrodynamic Forces on Pipelines: Model Tests, Prepared for PRCI by the Danish Hydraulic Institute, Dec-1986
- PR-170-716, Hydrodynamic Forces Acting on a Pipeline in an Open Trench, Prepared for PRCI by the Danish Hydraulic Institute, Jan-1988
- Ochi, M. K. and Hubble, E.N. Six-Parameter Wave Spectra, Proceedings 15th International Conference on Coastal Engineering, Honolulu, 1976
- Mardia, K. V., Statistics of Directional Data. London: Academic Press, 1972
- Borgman L.E., Directional Wave Spectra from Wave Sensors. In: Earle M.D., Malahoff A. (eds) Ocean Wave Climate. Marine Science, vol 8. Springer, Boston, MA, 1979
- Mardia, K.V., Some properties of clasical multi-dimesional scaling,Communications in Statistics – Theory and Methods, 1978
- PR-169-186
- PR-175-420
- Catalog No. L51570e, Contract PR-194-719, Energy Based Pipe-Soil Interaction Models, PRCI, June 1988
- PR-162-157
- PRCI Project PR-178-04405, Submarine Pipeline On-Bottom Stability Volume 1: Analysis and Design Guidelines, Kellogg Brown & Root, Inc., Dec-2008
- PRCI Project PR-178-04405, Submarine Pipeline On-Bottom Stability Volume 2: Analysis and Design Guidelines, Kellogg Brown & Root, Inc., Dec-2008
- Abdolmaleki, K. and Gregory, C. J., Performance of Pipe-Soil Interaction Models in a Quasi-Dynamic Approach to Pipeline Stability Analysis, OMAE-77988, 2018, Spain
- Jacobsen, V., Bryndum, M.B., and Bonde, C., “Fluid Loads on Pipelines: Sheltered or Sliding,” Proc. 21st Offshore Technology Conference, Paper No. OTC 6056, Houston, 1989
FAQ
-
Except for the Level 3, the software can be used for stability assessment of HDPE pipes.
The level 3 uses a beam-element type of finite element approach that takes the stiffness of the pipe into account. However, the software has only been applied to steel pipes and no validation has been conducted on using Level 3 for analysis of flexible pipes.
Therefore, it is not recommended to use Level 3 at this stage. Check Out
-
The reference level for current input in Level 3 is the elevation of the top of the pipe, including any coatings, and assuming no embedment.
The theory used to convert specified currents to the elevation of the top of pipe is at the discretion of the user. Check Out
-
In the PRCI OBS V3.0, the software could not receive water depths less than 6m.
In the PRCI OBS V4.0, this restriction has been removed and users can input any water depth. However, the applied theory has not been revised is still based on linear wave theory.
Therefore, it is the users’ responsibility to ensure that ratio between the inputted wave data at the given water depth does not exhibit very nonlinear / breaking wave scenario. Check Out
-
“Lateral factor of safety” means Horizontal Safety Factor at Theta.
The vertical factor of safety is computed but ignored. It is not significant if the pipe moves up and down slightly so long as it does not move horizontally as determined by the horizontal safety factor calculation.
Pipeline stability for Level 2 analysis requires that at the end of 4 hr storm buildup the horizontal safety factor at theta for U(1/100) must be 1 or greater and that at the end of the additional 3 hr storm the horizontal safety factor at theta for U(1/1000) must be 1 or greater. Check Out
-
This is the momentary ratio of hydrodynamic force and lateral resistance at each time history. Check Out
-
Currently, no way has been found to use the factor of safety as calculated in Level 3 as a pass/fail criterion like Level 2. Check Out
-
Consult section 5.8.4 from the version 4.0 User’s Manual:
Ramping force begins at t=0. To simulate slowly built-up dynamic forces use a “Build-up sea-state ramp” of 12 or less. Check Out
-
Preliminary stability analyses should be completed using Level 2 or the ASM module, so as to have a good starting point for a Level 3 stability analysis.
- For each pipe outer diameter and weight, sufficient runs need to be made with different “seeds”. Random seeds are numbers used as internal input to generate random irregular sea states, with two different seed values resulting in two different sea states. Performing the analysis with a sufficient number of storm simulation seeds provides a reliable indication of the range of results which may be obtained for the specified wave spectrum parameters. Check Out
-
No.
From the embedment point of view, it is realistic to assume that the cable has zero embedment, but the limitation of OBS is that it cannot capture the influence of free span zones on the cable’s lateral stability. Check Out
-
The software produces two vertical safety factors. One is corresponding to the minimum horizontal safety factor at wave angle “Theta” and the other one is the independently minimum vertical safety factor.
The lateral soil resistance includes a passive component, which is solely dependent on the pipe embedment.
In scenarios where lift force momentarily gets larger than the Submerged weight, the vertical safety factor < 1 and the pipe might lose contact with seabed, however, the embedment related component of the passive soil can remain nonzero. Check Out
-
If you receive an Illegal Operation! message when switching between Levels, this could provide a workaround for you. Check Out
-
If you are trying to activate OBS Version 4.0 and receive an error message, this quick guide should help us gauge where the root of the issue is and how best to resolve this for you. Check Out