Preventative Measures to Control Corrosion Pitting
Corrosion Rates
A corrosion rate needed to set the re-inspection interval, reassess the performance metrics and their current applicability, plus to ensure the assumptions made are correct. At each direct examination where corrosion pitting is found, the operator should measure and record each pitting cluster. The aforementioned data are then used to estimate corrosion rates. Average corrosion rates are related to the environment, depth of pitting and years of in-service.
Example: Direct examinations should be made locations from ILI, Direct Assessment, or areas of concern in which metal loss or coating faults have been found. Metal loss defects found during each direct examination should be measured, documented, and mitigated. These data can be used to estimate corrosion rates. One method is to use average corrosion rates related to soil resistivity as provided in the following table:
Table for Corrosion Rates Related to Soil Resistivity
Corrosion Rate (mpy) | Soil Resistivity (ohm-cm) |
---|---|
3 | > 15,000 + no active corrosion |
6 | 1,000 – 15,000 and/or active corr |
12 | < 1000 (worst case) |
16 | Unknown or No Information |
The user determined a 6 mpy corrosion rate that was based on 1,500 ohm-cm soil with active corrosion. The pipeline consisted of a 26-inch O.D., 0.500-inch W.T., 52,000 SMYS, pipeline operating at an established 1160 MAOP.
See Figure 1 below, which illustrates example calculations held within the RSTRENG+/ECDA software applications on our HUBPL platform. With the corrosion growth rate entered into the data input tab, preventive and predictive integrity/corrosion solutions can be determined. Specifically, one can determine the time until failure for the pipe, remaining life of pipe, and re-assessment interval of the pipeline. Furthermore, the reporting feature will enable the user to generate an intuitive, comprehensive reports that engineers and technicians can easily read and understand.
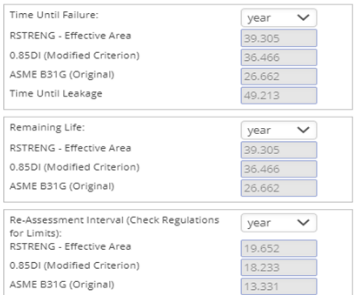
Re-Assessment Intervals
Re-assessment intervals are to be defined on the basis of scheduled indications as per ASME B31.8S.
- All indications will need been addressed during direct examinations of the piping and must be prioritized.
- Based on the area/location of the piping, the remaining indications are expected to experience less growth. This should be prioritized based on lesser corrosion rate.
- Once these areas of concern have been identified, they must be repaired by the next re-inspection period.
The conservatism of the re-assessment interval is not easy to measure because there are uncertainties in the remaining flaw sizes, the maximum corrosion growth rates, and the periods of a year in which defects grows by corrosion. To account for these uncertainties, the re-assessment interval defined herein is based on a half-life concept. An estimate of the true life is made, and the re-assessment interval is set at half that value.
The maximum re-assessment interval shall be taken as one half of the calculated remaining life. The maximum re-assessment interval may be further limited by documents such as ASME B31.4, ASME B31.8 or NACE SP0502.
Corrective Measures to Control Corrosion Pitting
RSTRENG provides the information for an operator to effectively allocate resources for appropriate prevention, detection and mitigation activities that will result in improved safety and a reduction in the number of incidents. The ultimate goal of assessing metal loss is to identify the most significant corrosion so that an operator can develop an effective and prioritized prevention/detection/mitigation plan to address the risks.
Therefore, using RSTRENG analysis and reports for determining integrity assessment intervals and mitigation (repair and prevention) methods is the right tool for performance-based integrity management programs which save time and money.