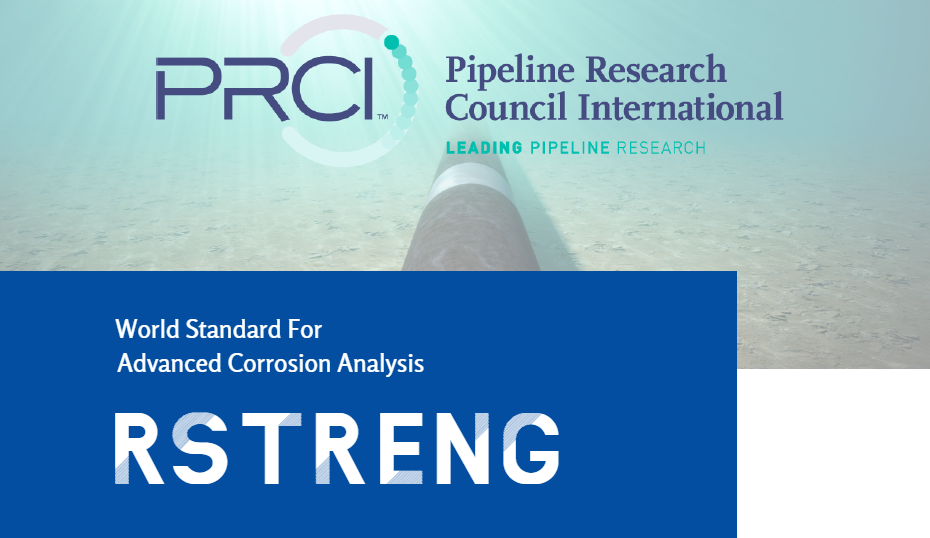
The RSTRENG© Application Guide presents information, guidelines, and procedures for use during operations and integrity tasks for field or office applications.
This tool combines RSTRENG©, B31.G, Modified B31.G into one toolbox. Additional calculations can also be added to the module such as DNV, API 579 Level 1, Shell 92, and PCORR.
Getting Started
- User Settings
- Data Input
- Profile
- Corrosion Profile – Corrosion Depth
- Calculations
- Non-PRCI Calculations
- Remaining Life & Reassessment Interval
- RSTRENG +
Key Highlights
The RSTRENG© program consists of multiple upgrades that assist the user to make faster and better decisions in the field or office. Some of the highlights of RSTRENG© include the following:
- Enhanced graphics to assess the corrosion pitting from short to long lengths.
- Unlimited data points to assure that new technologies such as 3D tools can assess. 1000’s of increments and depths for a more accurate assessment of pressure calculations.
- Provides safety while meeting the regulations
- Provides the Zero Out Method to avoid unnecessary cut-outs
- Ability to determine all effective lengths in long areas of corrosion for repair, whereas other programs do not identify these multiple effective lengths.
- Zeroing out multiple effective lengths in long length corrosion i.e. 80 inches
- Show each effective length for each step of the way
- Ability to determine re-assessment intervals and remaining life calculations based on corrosion growth rates.
- Written into CFR 192 and 195 as the only approved remaining strength program for pipeline operators.
- Meets being Traceable, Verifiable, and Complete (TVC) by PHMSA
- Record keeping and retrieval to meet Big Data requirements
- Track locations using the HUB
- Produces Reports and allows comments up to 850 characters.
- Ability to determine
- Failure Pressure Ratio
- Time Unit Failure
- Remaining Life
- Re-Assessment Interval
- Potential Impact Radius
Pipeline operators use PHMSA approved RSTRENG© program that is specified in the pipeline industry Code of Federal Regulation (CFR). Technical Toolboxes is the sole provider of the official RSTRENG© program. B31.G, Modified B31.G, and RSTRENG© will now be referred to as RSTRENG© providing the user with all necessary tools, including RSTRENG© to assess, analyze and assist in the mitigation of the effects of blunt metal loss corrosion defects.
In addition, Technical Toolboxes provides programs that consist of training and testing for those individuals seeking technical RSTRENG© certification for Pipeline Integrity Inspectors, Technicians, and Engineers to assess corrosion and related blunt defects.
Application Overview
When internal or external corrosion features in pipelines are detected by in-line inspection (ILI), ECDA, or other maintenance activities, a decision to replace, repair, or accept and monitor each feature must be made. This decision is based on the prediction of the failure pressure of the corroded pipeline and must adhere to the US Code of Federal Regulations (CFR) Title 49, Parts 192 and 195, which stipulates that ASME B31G or RSTRENG be used to assess the remaining strength of corroded pipelines.
The original research and development were conducted by PRCI. RSTRENG is currently the preferred technology for determining the remaining strength of externally corroded pipelines, as it provides a more accurate assessment of the corroded area than ASME B31G and Modified ASME B31.G. This results in enhanced pipeline integrity and safety while simultaneously lowering costs to the pipeline owner/operator. For additional information about AC interference and mitigation, please see the report that is furnished by Pipeline Research Council International, Inc. (PRCI) “PRCI PR-200-9414” on this link.
Program And Variable Limitations
CORROSION — The deterioration of a material such as carbon steel due to its environment.
DIAMETER (dia.) — The diameter, D, is the outside pipe diameter, and has units of inches. The range of D is 2.0000 to 42.000 in. The default value is D = 12.750 in.
DESIGN FACTOR (F) — Although 49 CFR 192 or 195, establishes a design factor, F, the user can input another F value. The range for F is from 0.10 to 1.00. The default design factor is F = 0.72.
LONGITUDINAL JOINT FACTOR (E) — The longitudinal joint factor, E, depends on the type of pipe welds. The input screen limits E to either 0.60, 0.80, or 1.00, consistent with the values. given in 49CFR192, Section 192.113. The default value is E = 1.00
MAXIMUM ALLOWABLE OPERATING PRESSURE (MAOP) — The maximum allowable operating pressure, MAOP, is used as the design internal pressure for calculating circumferential stress due to internal pressurization and has units of psi. The range for MAOP is 0000 to 5000 psi.
SPECIFIED MINIMUM YIELD STRENGTH (SMYS) — The specified minimum yield strength, SMYS, has a range of allowable values covering steel grades A25 (SMYS = 25000 psi) to X-80 (SMYS = 80000 psi). The SMYS is also used to establish the girth and longitudinal weld fatigue endurance limits.
WALL THICKNESS (wt.) — The pipe wall thickness, wt. has units of inches. The wall thickness to diameter ratios must be within the range of wt./D = 0.01 to 0.08.
ZERO OUT METHOD (ZOM) — This method is used when there are more than one effective area in long length pitting clusters such as in 30-inch length or greater up to a full joint of pipe to calculate the safe operating pressures.
Additional Resources
Technical Toolboxes offers training webinars on these upgrades as well as RSTRENG© on-site training with certification. RSTRENG© training courses are also offered with defect analysis understanding from half-day, one day, and one 1/2 days depending on your needs. Review our website under The training section to sign up for these courses.
MAOP To Be Used For RSTRENG Calculations
In both RSTRENG (See AGA/PRCI Research Report PR 3-805, included here as Reference (7), and ASME/ANSI (Part 4, Article 4.2) the maximum allowable operating pressure that must be used in the RSTRENG calculation is the greater of either the established MAOP or the pressure calculated by Barlow’s formula including design factor. The same pressure can be calculated using the equations from CFR Part 192 or Part 195, excluding a joint factor.
MAOP = (2St / D) F
Where:
S = SMYS(psi)
D = dia(in)
t = wall thickness(in)
F = design factor
If Corrosion < 20% of Wall thickness
- British Gas proposed a “no-failure” boundary and validated it using their own and AGA pipe burst tests.
- If a pipeline has corrosion that does not exceed 20% of the wall thickness, the pipeline may be left in service regardless of the length of the corrosion if the operating stress level is less than or equal to 72% of SMYS and the remaining wall thickness is at least 80% of that required by the design.
Summary: Modified B31G Criterion & RSTRENG
- Are accepted by US DOT/OPS, CFR Sections 192.485, 192.7, 192.933 for gas lines and 195.3, 195.452, 195.587 for hazardous liquid lines
- Both are less conservative than the Original B31G Criterion
- RSTRENG Automatically address complex corrosion geometry
- Both require fewer cutouts than the Original B31G
Validation efforts for RSTRENG
As we have discussed, the PRCI report prepared under Contract No, PR 3-805 was the basis and background for RSTRENG. The initial work was based on 86 burst tests, and subsequent to the generation of RSTRENG, an additional 82 burst tests were evaluated to continue the validation of RSTRENG. A significant number of these additional tests were performed on pipe that had the corrosion-simulating grooves machined.
This continued validation effort is presented in the PRCI report prepared under Contract No. PR 218-9304, “Continued Validation Of RSTRENG”, by Kiefner, Vieth, and Roytman. This report (Ref 8) is intended to provide qualitative validation to define applicability and limitations and quantitative validation to compare actual with predicted pipe failure pressures.
The continued validation efforts included comparing predicted test failure pressure using RSTRENG against actual failure pressures for the:
- Interaction of corroded areas
- Behavior of very long flaws
- Behavior and interaction of isolated pits
- Effects of diagonal/spiral corrosion
- Effects of patches of corrosion having significant longitudinal and circumferential extent
- Effects of large axial stresses on the behavior of corroded pipe
- The following series of slides summarize a large part of the continued validation effort.
RSTRENG Effective Area
- Level 2 evaluation a number of pit depths and spacing measurements are required for a projected profile of metal loss. Each additional corrosion depth entered in a profile increases algorithmically the number of sub-sections that can be evaluated.
- More than one profile may be necessary for agreement on the lowest failure stress of an area of multiple patches and pits.
- Interaction rules must be used as applicable
References
- PRCI – A Modified Criterion for Evaluating the Remaining Strength of Corroded Pipe
- PRCI – Database of Corroded Pipe Tests
- PRCI – Continued Validation of RSTRENG
- For additional information please see reports that are furnished by Pipeline Research Council International, Inc. (PRCI) using the following link. https://www.prci.org/Research/Corrosion/CORRProjects/EC-6-1/4153/15495.aspx
- NACE Standard RPO102 (latest revision), “In-Line Inspection of Pipelines” Houston, TX
- NACE Standard RP0313 (latest revision), “Guided Wave Applications for Pipelines”, Houston, TX
- NACE Standard RP0502 (latest revision), “Pipeline External Corrosion Direct Assessment Methodology”, Houston, TX
- ASME B31.8 (latest revision), Gas Transmission and Distribution Piping, New York, New York
- ASME B31.8S (latest revision), Gas Transmission and Distribution Piping, New York, New York
- ASME B31.G (latest revision), ASME B31G – Manual for Determining the Remaining Strength of Corroded Pipelines (RSTRENG), New York, New York
Appendices
- Remaining Strength of Corroded Pipe (RSTRENG) Assessment Procedure, Joe Pikas
- Preventative Measures to Control Corrosion Pitting, Joe Pikas
FAQ
-
Technical Toolboxes receives many RSTRENG questions throughout the year; however, most of them are not related to operating the software. These questions are related to procedures, definitions, and field repairs.
When metal loss features in pipelines are detected by in-line inspection (ILI), a decision to replace, repair, and assess remaining features. This decision is based on the prediction of the failure pressure of the corroded pipeline and must adhere to the US Code of Federal Regulations (CFR) Title 49, Parts 192 and 195, that stipulates that ASME B31G or RSTRENG be used to assess the remaining strength of corroded pipelines. Check Out
-
What Actions must be Taken to Address Integrity Issues?
According to DOT 192.933 a calculation of the remaining strength of the pipe shows a predicted failure pressure less than or equal to 1.1 times the maximum allowable operating pressure at the location of the anomaly. Suitable remaining strength calculation methods include, ASME/ANSI B31G; RSTRENG; or an alternative equivalent method of remaining strength calculation. Check Out
-
A corrosion rate needed to set the re-inspection interval, reassess the performance metrics and their current applicability, plus to ensure the assumptions made are correct. At each direct examination where corrosion pitting is found, the operator should measure and record each pitting cluster. The aforementioned data are then used to estimate corrosion rates. Average corrosion rates are related to the environment, depth of pitting and years of in-service. Check Out
-
Internal corrosion is most likely to occur where water first accumulates. Predicting these locations of water accumulation serve as a method for prioritizing local examinations. Predicting where water first accumulates requires knowledge about the multiphase flow behavior in the pipe requiring certain data. The following are some general calculations based on flow conditions. Keep in mind that these are strictly estimates and do not consider the effects of temperature, wettability, MIC, pressure, hydrocarbon characterization, gas composition, etc. Check Out
-
All corrosion defects found during each direct examination should be measured, documented, and remediated as needed. At each excavation, the pipeline operator should measure and record generic environmental characteristics (such as soil resistivity, hydrology, drainage etc.). These data have been used to estimate corrosion rates. Average corrosion rates related to soil resistivity are below in the following table with no CP. Check Out
-
ASME B31.G Original and Modified (0.85) are Level 1 assessment along with most other metal loss calculations that are limited to pits and short lengths of pitting clusters. Check Out